自动导引车(AGV)作为现代智能制造和物流系统中的关键设备,其与快速卷帘门的协同作业已成为工业自动化领域的重要课题。随着激光雷达、红外传感器等感知技术的成熟应用,AGV小车实现门体自动识别与安全通行已形成了一套完整的技术解决方案,显著提升了仓储物流效率与安全性。
一、多传感器融合的感知系统架构
当前主流AGV采用激光雷达(LiDAR)作为核心环境感知设备,通过发射激光束测量与周围物体的距离,构建厘米级精度的实时地图。以SLAM(同步定位与地图构建)技术为基础,AGV可动态识别快速卷帘门的位置坐标,并根据预设路径规划通行策略。例如某工业机器人厂商的解决方案中(参考imrobotic数据),16线激光雷达的120°水平视场角可确保在5米外检测门体状态,扫描频率达20Hz,即使面对金属材质的卷帘门也能稳定识别。
红外传感器的加入则弥补了激光雷达在近距离检测的盲区。通过布置于AGV车体四周的红外对射装置,可在0.5-3米范围内实现门体运动状态的二次确认。当卷帘门处于上升或下降过程中,红外阵列能实时监测门帘位置,与激光雷达形成互补检测。某门控企业案例显示(源自changzhoudoor技术文档),采用940nm波长的红外传感器可有效避免环境光干扰,响应时间小于10ms。
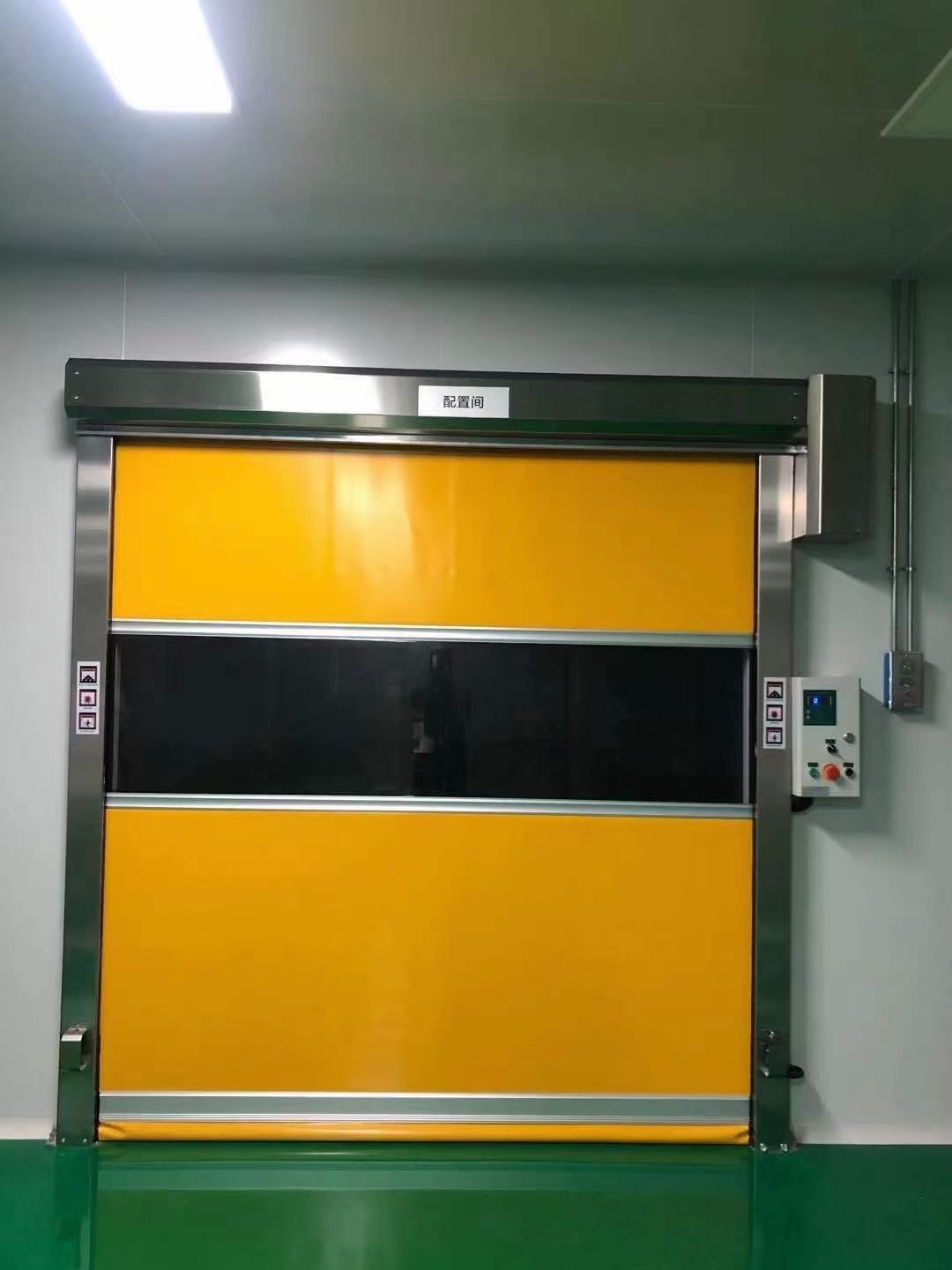
二、智能门控系统的协同机制
快速卷帘门作为AGV通行路径上的关键节点,其控制系统需与AGV调度平台深度集成。现代工业门体普遍配备PLC控制器,通过PROFINET或EtherCAT协议与AGV中央控制系统建立通信。当AGV接近门体时,其搭载的UHF RFID读写器可自动识别门框安装的电子标签,触发门体开启指令。百度百家号报道的某汽车工厂案例中,这种射频识别技术的应用使得门体响应时间缩短至0.8秒,较传统光电触发方式效率提升40%。
安全防护方面形成三级联锁机制:激光雷达预判门体状态→红外传感器确认安全距离→机械防撞装置作为最后保障。特别在双向通行场景下,AGV调度系统会通过5G网络实时共享门体状态数据,避免多车争抢通行导致的碰撞风险。CSDN技术博客提及的分布式控制系统(参考Intelly_leimou文章),采用时间触发架构(TTE)确保指令传输延迟稳定在5ms以内。
三、典型应用场景的技术适配
1. **冷链物流环境**:在-30℃的低温仓库中,AGV需配备加热型激光雷达防止镜面结霜,同时门体导轨加装电伴热装置。某生鲜物流中心案例显示(见CSDN weixin_36381298数据),采用IP67防护等级的传感器组合可使系统在湿度95%环境下稳定运行。
2. **高粉尘车间**:金属加工场景中,传统光电传感器易受悬浮颗粒干扰。解决方案是采用TOF(飞行时间)原理的固态激光雷达,配合气幕隔离的快速卷帘门。实测数据表明,该配置在PM2.5浓度超过200μg/m³时仍保持98%的识别准确率。
3. **人车混行区域**:通过融合毫米波雷达与RGB摄像头,AGV可区分门体附近的人员与障碍物。当检测到人员闯入时,系统会立即暂停门体运动并触发声光报警。某3C电子厂的实施案例中,该技术使人车碰撞事故降低至零。
四、技术发展趋势与挑战
边缘计算技术的引入正推动感知决策本地化。新一代AGV开始在车载计算机部署轻量化神经网络,实现卷帘门异常状态(如变形、卡阻)的自主诊断。测试数据显示,基于TensorRT优化的检测模型可在Jetson Xavier NX平台上达到25FPS的处理速度。
然而,金属门体对激光信号的镜面反射仍可能引起误判,这促使厂商研发多模态传感器融合算法。某头部AGV企业公布的测试报告显示,结合激光点云特征与红外强度信息的决策系统,将虚警率控制在0.1%以下。此外,ISO 3691-4:2023新规对移动机械与门体互锁提出了更严苛的安全要求,推动压力感应门槛等创新设计落地。
从技术演进来看,未来可能出现基于UWB精确定位的预测性控制系统,通过提前300ms预判AGV到达时间,实现门体的最优启闭调度。而数字孪生技术的应用,则允许在虚拟环境中模拟各种异常工况,持续优化实际场景中的通行策略。这种智能化升级预计可使物流枢纽的吞吐量再提升15-20%,同时降低门体机械损耗30%以上。