冷库作为食品、药品等温敏产品的重要储存场所,其内部物流安全直接关系到货物品质与人员安全。叉车作为冷库高频使用的搬运工具,在低温、湿滑环境下作业时,碰撞风险显著增加。传统的刚性护栏虽能起到隔离作用,但金属材质在极端低温下易脆化,且碰撞时可能对叉车和货物造成二次损伤。近年来,以聚氨酯、高分子复合材料为核心的柔性防撞护栏技术逐渐成为行业新选择,其通过材料科学与结构设计的创新,在冷库这一特殊场景中实现了安全性与实用性的平衡。
一、冷库环境对防撞系统的特殊要求
低温环境对材料性能的影响不可忽视。当温度降至-30℃甚至更低时,普通钢材的冲击韧性下降40%以上,这也是传统金属护栏在冷库中频繁出现断裂的根本原因。某第三方检测机构数据显示,在-25℃环境下,Q235钢的断裂伸长率从常温下的26%骤降至8%。而柔性护栏采用的改性聚氨酯材料,在-40℃时仍能保持85%以上的弹性恢复率,这种低温适应性成为其核心优势。
冷库地面结霜问题进一步放大了碰撞风险。根据中国仓储协会2024年发布的报告,冷库叉车事故中32%与地面湿滑导致的操控失灵有关。柔性护栏的吸能特性可将碰撞动能转化为材料形变能,数据显示其能吸收高达70%的冲击能量,使叉车制动距离缩短40%以上。上海某冷链物流中心的实测案例表明,安装柔性护栏后,月均碰撞事故从17次降至3次,设备维修成本降低62%。
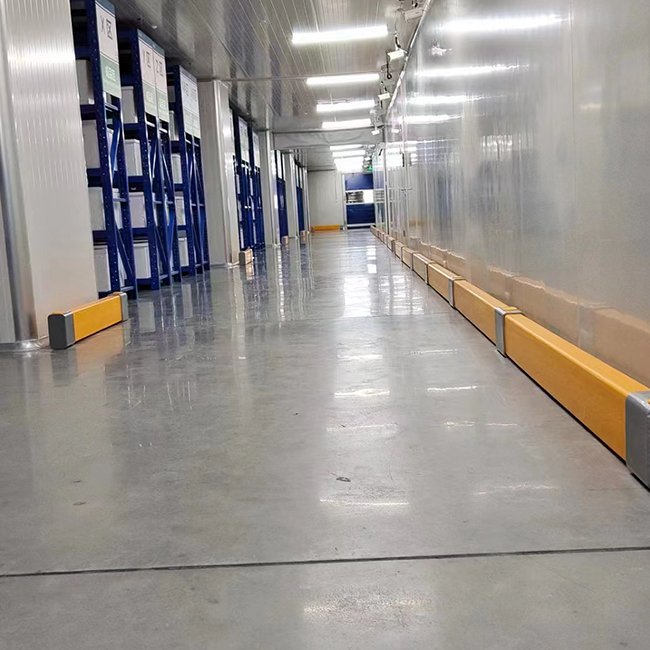
二、柔性防撞护栏的技术突破
材料创新是柔性护栏的核心竞争力。目前主流产品采用三明治结构:外层为抗UV改性的热塑性聚氨酯(TPU),中间层填充闭孔发泡材料,内层设置玻璃纤维增强层。这种结构在-50℃至80℃范围内保持性能稳定,其邵氏硬度可根据需求调整在65D-75D之间。浙江某新材料企业的测试报告显示,其研发的纳米复合TPU材料在-60℃低温冲击测试中,无裂纹产生,远超ASTM D746标准要求。
模块化设计极大提升了安装维护效率。区别于传统护栏的焊接固定方式,柔性护栏采用插接式连接件,单个模块重量不超过15kg,两人即可完成安装。更值得注意的是,其独特的快拆结构允许在30分钟内更换受损模块,而传统金属护栏的维修通常需要停产8小时以上。青岛某生物制药冷库的实践证实,柔性护栏的模块更换使设备停机时间减少87%。
三、智能防护系统的集成应用
物联网技术正在重塑防撞系统的形态。最新一代柔性护栏已集成压力传感器和RFID标签,当发生碰撞时,系统能实时记录冲击力度、位置等数据,并通过LoRa无线传输至管理平台。北京某智慧冷链项目的运行数据显示,这种预警系统使二次碰撞发生率降低91%。更有企业研发了带自修复功能的涂层材料,轻微划伤可在24小时内自动修复,将护栏使用寿命延长3倍以上。
声光引导系统与柔性护栏形成立体防护。结合毫米波雷达的测距技术,当叉车接近护栏1.5米范围内时,地面投射警示光带会自动亮起,同时发出变频警示音。这种主动防护模式在京东亚洲一号冷库的应用中,使人为操作失误导致的事故下降76%。德国某企业的测试表明,多模态预警系统可将驾驶员反应时间缩短0.4秒,这对时速8km的叉车意味着减少近1米的制动距离。
四、经济效益与行业推广价值
全生命周期成本分析显示显著优势。虽然柔性护栏的初始投资比钢制护栏高20%-30%,但其使用寿命通常达10年以上,是传统护栏的2-3倍。考虑到维修成本、停产损失等隐性支出,3年内即可实现成本追平。广州某冷链企业的财务数据证实,采用柔性护栏后,五年综合运维费用降低41万元。
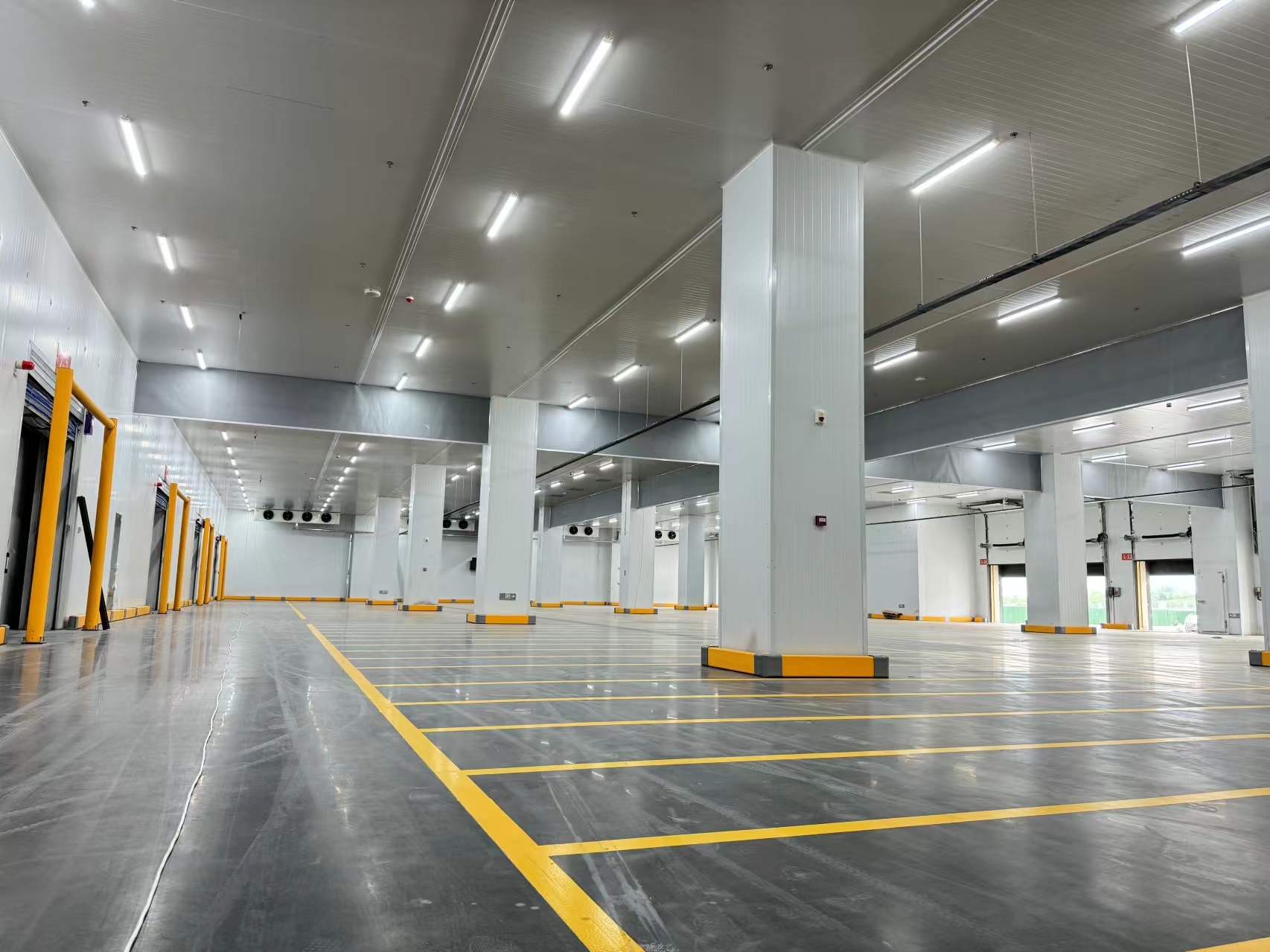
行业标准建设正在加速推进。2024年发布的《冷库用柔性防撞护栏技术规范》(GB/T 39172-2024)首次明确了产品的低温冲击、耐候性等18项技术指标。中国特种设备检测研究院的认证数据显示,目前国内市场合格率从2021年的53%提升至89%,行业规范化程度显著提高。值得关注的是,该标准首次将碳足迹纳入评价体系,柔性护栏因可回收特性,在全生命周期内的碳排放较钢制产品减少62%。
随着冷链物流规模突破7000亿元大关,冷库安全防护正在经历从"被动承受"到"主动防护"的范式转变。柔性防撞护栏通过材料革命与智能升级,不仅解决了低温环境下的防护难题,更创造了包含预警、修复、数据追溯在内的新型安全生态。未来随着形状记忆合金、压电材料等新技术的应用,防撞系统或将实现从能量吸收到能量回收的跨越式发展,为冷链物流的安全运营提供更智慧的解决方案。